Water and Fire Damage Restoration in Wheeling, WV
24/7 Water & Fire Restoration Services
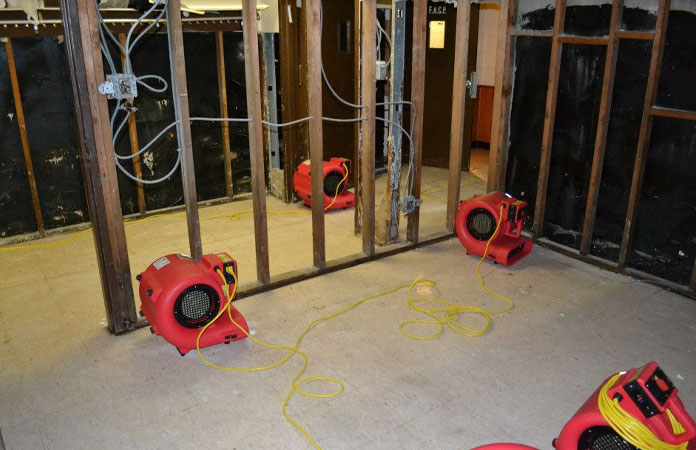
When faced with water or fire damage on your property, Panhandle Cleaning and Restoration provides top-notch services with various guarantees. Our comprehensive water and fire damage restoration services include efficient water extraction, meticulous water and fire damage cleanup, thorough drying and dehumidification, and effective damage repairs, restoring your space to its pre-loss condition. Our commitments encompass:
- Free water and fire damage inspection & cleanup estimate
- 24/7 emergency water removal and fire response services
- Flood damage cleanup
- Water and fire damage repairs
- Sewage backup cleanup
- Emergency fire board up
- 60-minute response time
- 100% guarantee on the quality of our services
Common Causes Of Water Damage
Water damage can be caused by a variety of issues, ranging from minor leaks to major floods. Even small issues can escalate if not addressed promptly, leading to significant damage and costly repairs. Panhandle Cleaning & Restoration has years of experience in handling all types of water damage. We help both homeowners and business owners recover from water damage caused by the following issues:
Whatever the cause, contact Panhandle Cleaning & Restoration for prompt action on your water damage emergencies. We have the expertise to handle any water damage situation, whether it's a major incident or a minor issue. No matter the size of the project, we’ve got you covered.
Water Damage Restoration Process
Fire Damage Restoration Process
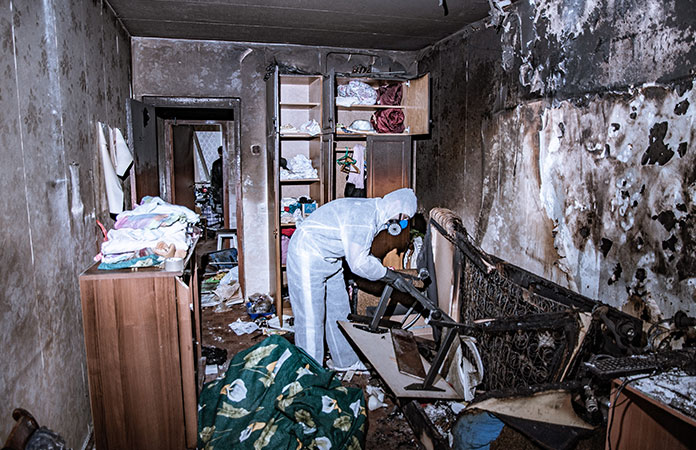
Smoke Soot Cleaning & Smoke Deodorization
Our comprehensive restoration services include the extraction of standing water left by the fire department, as well as the removal of smoke and soot residue. We aim to eliminate any lingering traces of a fire, allowing you to proceed with your life confidently.
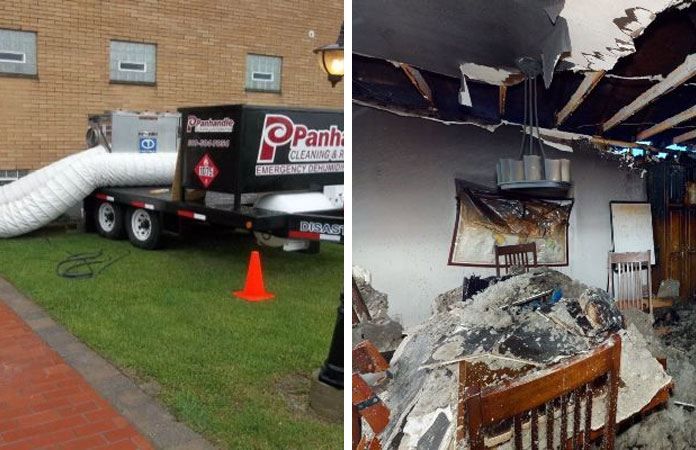
Does Homeowners Insurance Cover Water and Fire Damage?
Typically, water and fire damage fall under the coverage of your standard homeowner’s insurance policy, with some exceptions, such as natural disasters leading to significant flooding. If your residence suffers flood-related damage, you may require a distinct flood damage insurance plan. Most other types of damage, unless stemming from severe negligence, are generally covered.
When you choose to collaborate with Panhandle Cleaning & Restoration, we have established connections with your insurance provider and possess the expertise to optimize your coverage. Contact us today to initiate the process.
Rely on Us for the Best Restoration & Remediation Services in Wheeling
When your property in Wheeling has been damaged by fire, flood, or mold growth, we are the company to contact to get your property and your life back in order. For almost 50 years, Panhandle Cleaning & Restoration has set the local industry standard for top-notch services for all types of restoration and remediation-related activities. We also handle homebuilding & home remodeling services, along with biohazard cleanup, rain gutter installation, smoke damage restoration, and more. To learn more about our company and our services, call 866-515-2364 or click here to schedule services ASAP at your property in Wheeling.